Tap into IoT’s unfulfilled market potential
Authors: Michele Turitto - Managing Partner, Industrial and Graham Lodge - Principal Consultant
Early predictions surrounding internet of things (IoT) uptake may have been over optimistic, but it’s still enjoying a robust growth trajectory. The latest global forecast from IoT Analytics indicates that around 19 billion IoT devices are installed worldwide, and suggests a huge amount of unfulfilled potential.
So, how can industrial, chemical, and energy companies identify, and unlock, new IoT opportunities? Designing systems that deliver tangible value is key.
Look beyond technical enablers of IoT
Building blocks for IoT have evolved at pace. From better sensors and feature-rich microcontrollers to micro energy harvesters and low-power radio networks. The rise of cloud-based computing power is another key enabler. Yet technology alone is not enough to unlock IoT’s full value. Systems also require a holistic design approach. It’s about blending the best technical capabilities for specific use cases to create credible, cost-effective solutions to real-world needs.
Industrial IoT systems typically involve a population of endpoint devices. In an ideal world, these devices would be simple to attach / retrofit in the target location. They would also find the host network automatically, pre-process any sensor data onboard, and have no ongoing maintenance costs other than data collection. In reality, installation and management of endpoint devices involves trade-offs and compromise.
Considering the following factors can help strike a balance between cost and performance so IoT systems deliver high-value outcomes:
-
Choose the best energy source
In non-IoT applications, design decisions related to a device’s power source are usually straightforward. However, in the highly constrained world of IoT endpoints, things are more nuanced:
- Taking wired power from a nearby source can be the lowest-risk design choice. However, wired power incurs additional installation cost, and it’s not always feasible, for instance in remote locations, or on rotating machinery or body-worn sensors. Onboard power is therefore preferable for many devices, especially if data connection is also wireless
- Onboard batteries have been used with notable success in some industries. Sagentia Innovation has developed products for water and gas metering where LiThCl batteries can power a smart meter for >10 years. But batteries are difficult to characterise, underperform in harsh environments, and eventually need replacement. Swapping out batteries in the field is inconvenient and can incur significant service costs.
- Onboard energy harvesting can provide a zero-maintenance power source, but the source may be intermittent, or unable to cope with high peak power demands. Product design effort and manufactured cost depend on the size and type of the harvesting element (photovoltaic, thermoelectric, etc). In the early days of IoT, energy harvesting was confined to devices with the lowest power use. However, implementation is getting easier. Several semiconductor majors now provide highly optimised energy harvesting ‘front end’ chips, capable of charging a supercapacitor or micro battery from a tiny energy source. The host device can then use the stored energy in short bursts, at a much higher power level.
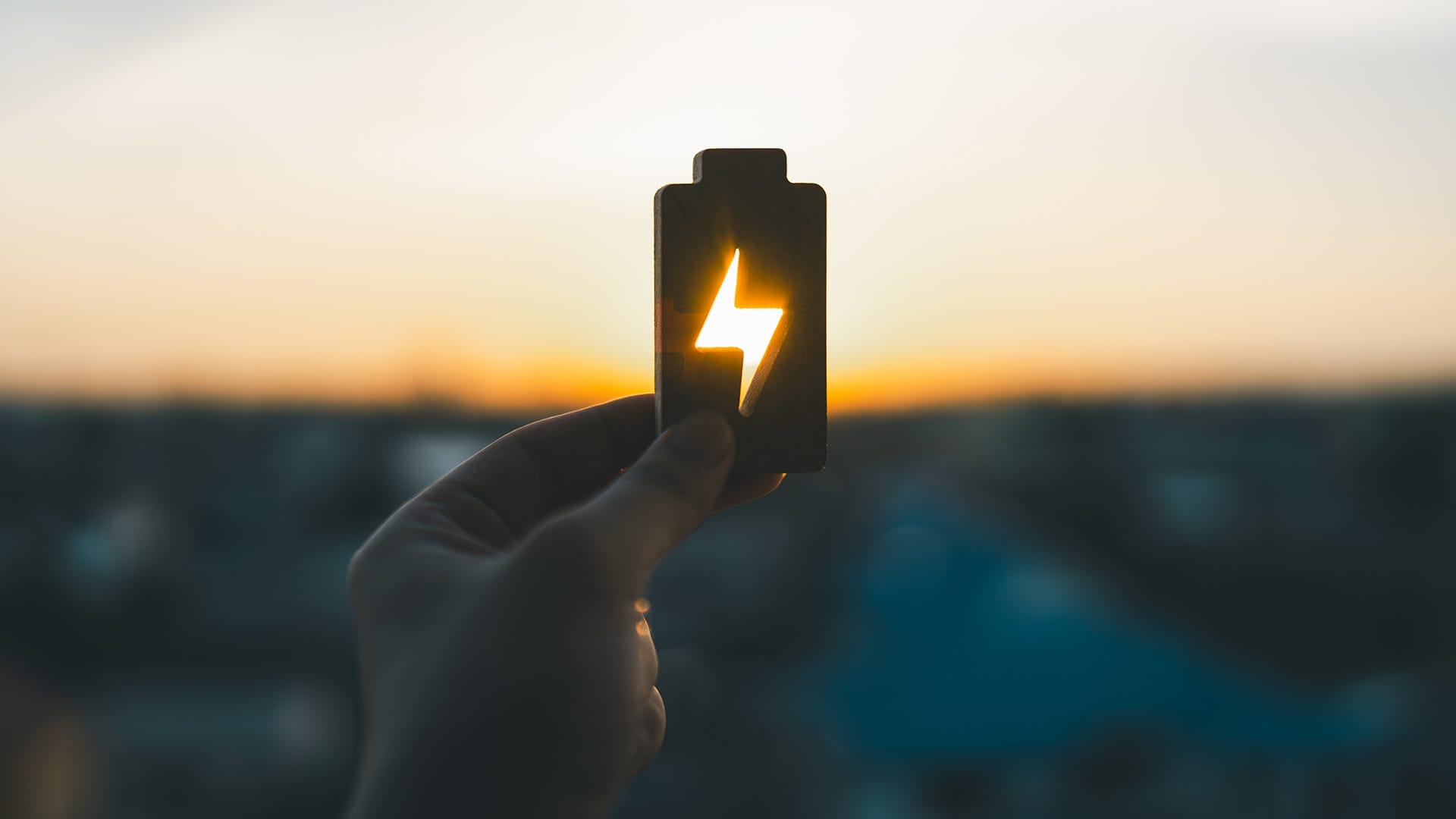
-
Reduce energy requirements
An alternative to improving an IoT device’s power source is to reduce its energy requirements. Whether the power source is a small photovoltaic element, a coin cell, or even a large lithium battery, the same high-level considerations surrounding energy needs apply. Design engineers should challenge and clarify operational requirements (sensing, storage, networking) and think in terms of the entire device lifecycle:
- Manufacturing: does the device require an active DC source for testing or calibration?
- Supply chain: can the device be placed in deep sleep or can power be disconnected until installation?
- Installation: does the energy source impose additional positioning or mounting constraints?
- And so on, through each phase of device life, across normal everyday operation, in-field updates, fault response, and eventual disposal.
Once the high-level endpoint design is settled, we find that implementation usually requires systematic, solution-specific optimisations. This demands tight coordination between engineering disciplines to work through the inevitable compromises. Targets generally include reducing the sample rate, selectively powering down sensors/comms circuits/display elements between samples (while ensuring they can rapidly wake again), optimising software execution time, using lowest-power microcontroller sleep states, and managing a highly constrained user interface.
-
Optimise edge vs cloud processing
Simple sensor nodes such as utility meters, or those monitoring slow-changing signals (e.g., water pressure, building temperature, humidity), are good candidates for battery operation or harvested energy. They require minimal processing to condition or draw insights from the sampled signals, and this is easily performed by a small CPU at <1mW average power.
For sensor nodes acquiring higher bandwidth signals and/or performing more complex processing (e.g., a machine-condition monitor ‘listening’ to a vibration signature) energy requirements are higher. Designers often assume the processing algorithm can be refined over time, possibly using machine learning to inform improvements based on a large population of sensors. But this may require sending real-time data to the cloud for processing on a powerful central computer which supports large numbers of edge nodes.
There is an active industry conversation on where the balance lies between central processing (e.g. in the cloud) and edge processing (i.e., drawing insights at each sensor node). Benefits of edge processing include lower latency, reduced data bandwidth and lower storage costs. It can also improve data security. A potential downside is that adding more complex data analysis to a sensing node increases its power requirements. Meanwhile, the available hardware options are evolving: several manufacturers recently launched CPUs with architectures optimised for algorithms derived via machine learning.
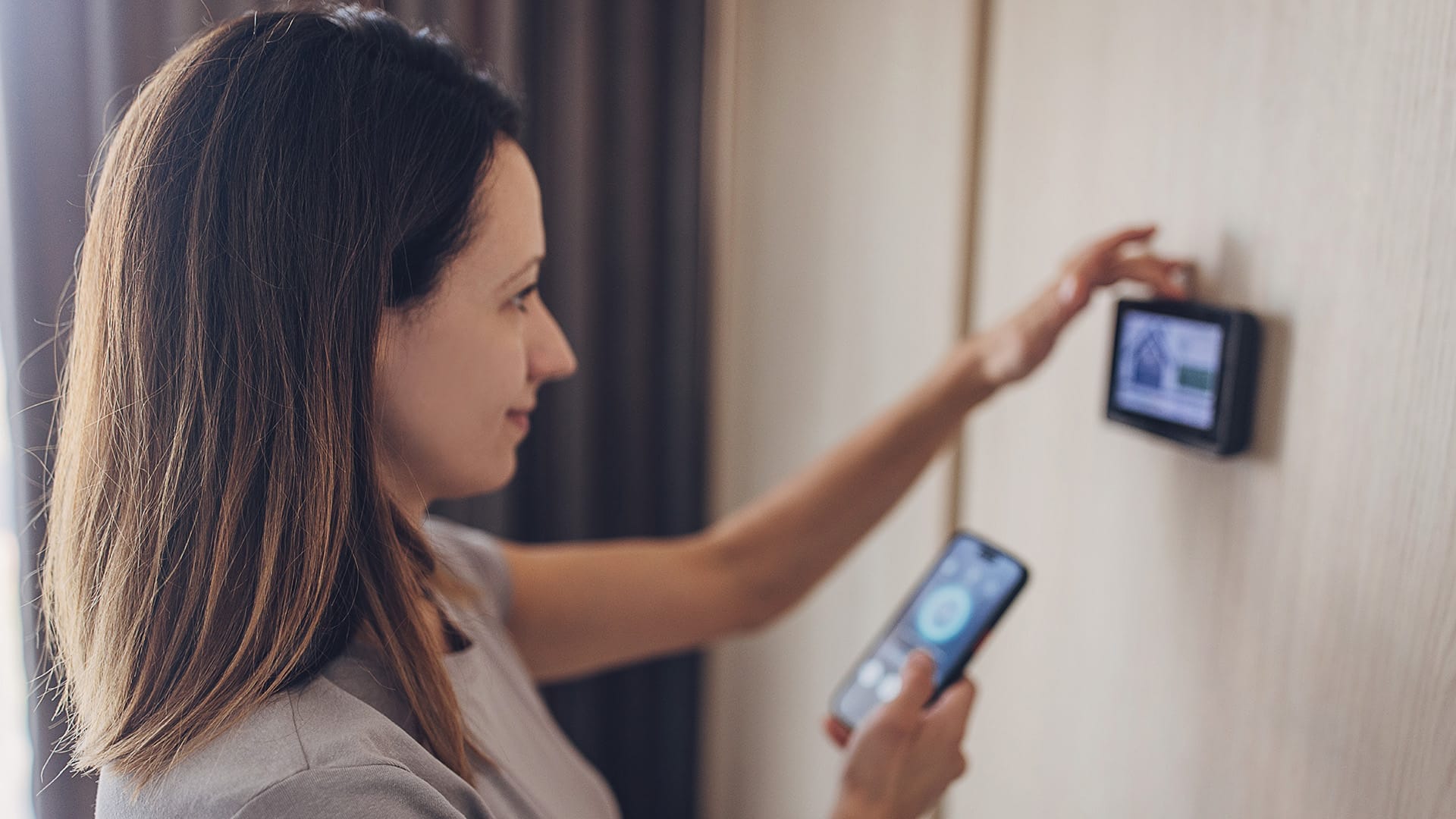
Make IoT devices’ energy budget central to design decisions
Ultimately, any product design must balance technical capability, cost, robustness, and other relevant factors. An additional challenge for IoT endpoints is weighting the energy budget against these constraints.
To realise the full potential value of IoT solutions, the following questions should be considered in parallel:
- What is the most effective energy source for my needs?
- How can power requirements be optimised?
- What is the correct edge/cloud processing balance for my application?
At Sagentia Innovation, we regularly address these questions for clients who are interested in industrial, energy, and chemical IoT applications.
Reach out today if you’d like support with your IoT development.